The smell of cheese and sweaty shoes wafted in the air as I disembarked from the car. Ahead of me, a large sign that says COCA-COLA AMATIL. Walking past the three safety signs that lead to the office, the tour was about to begin. As part of a hackathon sponsored by Coca-Cola Amatil, I recently got the opportunity to learn more about logistics and operations. A tour of the CCA distribution centre was included in the hackathon and did I have a fun time!
A fridge full of Coca-Cola Amatil products greeted us as we entered the office. We were issued high visibility vests and were required to sit through 10 minutes of safety briefing, coupled with some safety tests. I sipped on a juice box as we took the safety briefing test. After that, our tour began. Our tour guide was Mark Hopkins, One Logistics Project Manager of CCA. He started off by rattling off interesting facts about the distribution centre while I furiously typed away my notes on Google Keep.
He explained that the distribution centre is entirely covered in 500kW solar panels. It was an investment that only recently paid off with the building of the new preform plant. Prior to the preform plant’s construction, the solar panels were generating excess electricity during down times, but now that the preform plant – capable of making 750 bottles per minute; and runs 24/7 – has been built and is running constantly, they now use their energies efficiently enough. Then time came for us to actually enter the warehouse.
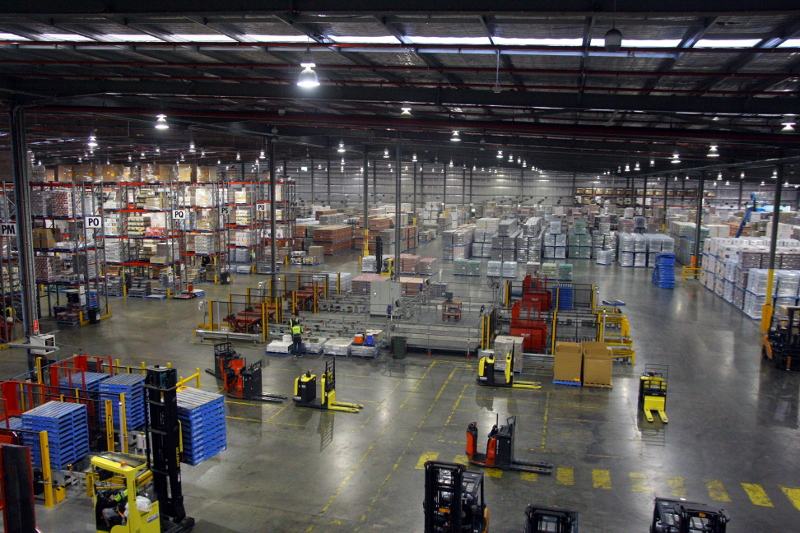
The size of the warehouse was indeed awe-inspiring. There was a sense of busy-ness as the forklift operators hustled and bustled around, carting crates to and fro on the warehouse floor. One can’t help but feel small, standing at the entrance of the warehouse looking inwards. The ceiling towered over us and powerful bright white lights shone down upon us like the sun. Well labeled multi-storey shelves not unlike those found in IKEA (except much taller) lined our left and a wide space filled entirely with pallets of goods filled our right. There were informal lanes of sorts for the forklifts to whizz past us. This only added to the sense of hustle. Right in the center of the warehouse was a pallet reloading system.
It was explained that the majority of stock in the shelf-less section of the warehouse are untouched by human hands. The process is automated to an awesome degree – from the unloading of trucks to the placement of product on the ground, everything is tracked, and done by robots. Accordingly, self-driving/guiding cranes would pack these. The reason for automation is simple: reduce human errors.
Although most of the stocking is done by machines, picking is mostly human driven. It is here that I witnessed a very good example of a Worse-is-Better system.
Worse is Better
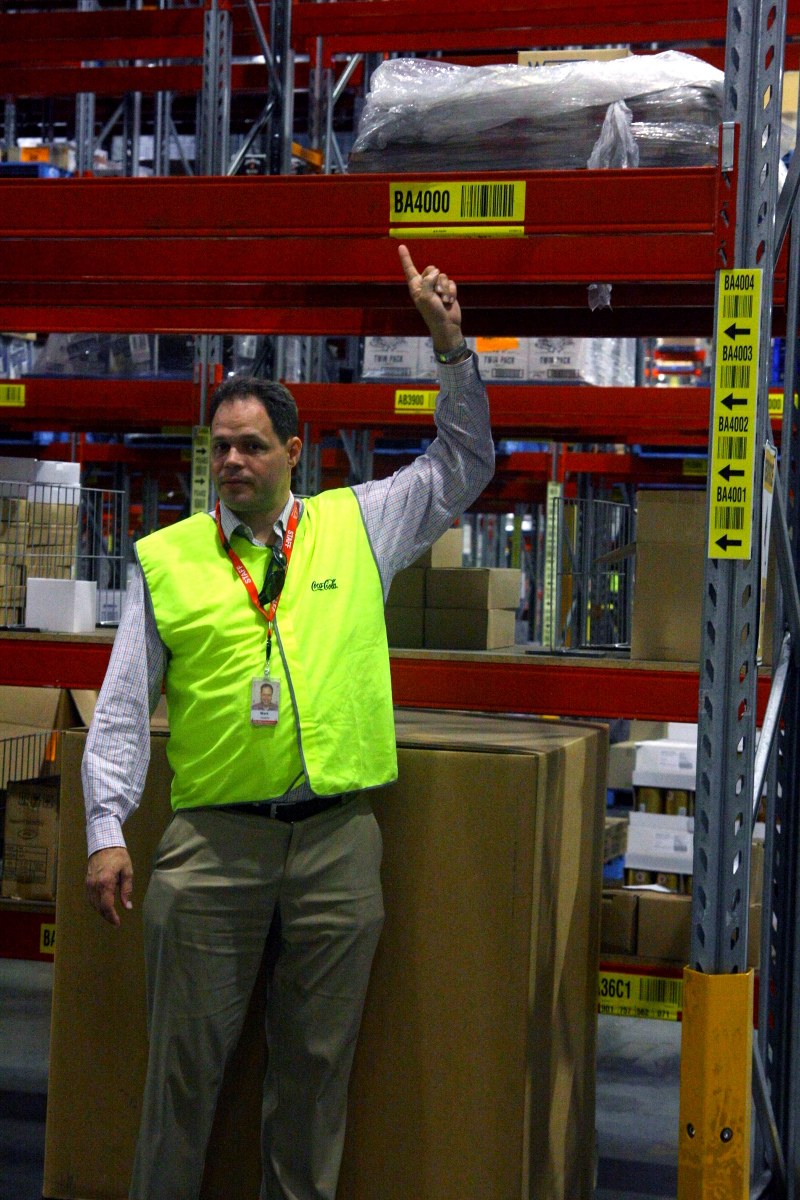
The system being used in the CCA Distribution Centre is a voice picking system. Every operator is fitted with a Motorola bluetooth headset, and basically receives instruction from a machine. The operator then goes to the shelf where the product is held, and then repeats a check digit to the machine. If the check digit is correct, the machine tells the operator the amount to pick. An example can be seen in this video (it’s not the one that CCA uses). The purpose of this is to reduce human errors. The operators do not have to know what products are in the cases on the shelves. Instead they just pick whatever ID is provided to them. The check digits are to confirm they’re at the right place and will be picking the right item. The odd thing that struck us was this: the check digits are printed on paper and pasted on the shelves. These numbers changes every few days, as operators would very quickly remember the digits and make errors.
Our tour group comprised of a number of software engineers and a few hackers. So immediately questions like “why not use a digital system” was floated. The history was then explained to us – they did in fact consider using that, but there were some cost and practical limitations to having a fully digital system, and so instead the old sticker method is continued instead. Other interesting stuff about the order picking system with check digits include the fact that the check digits used to be in much larger fonts. However that actually increased human errors in terms of order picking. A research had instead discovered that a font size of 14 points is the perfect size to minimize errors.
In fact, throughout the trip to the distribution centre, there were many examples of worse-is-better systems being used.
Continuing the Tour
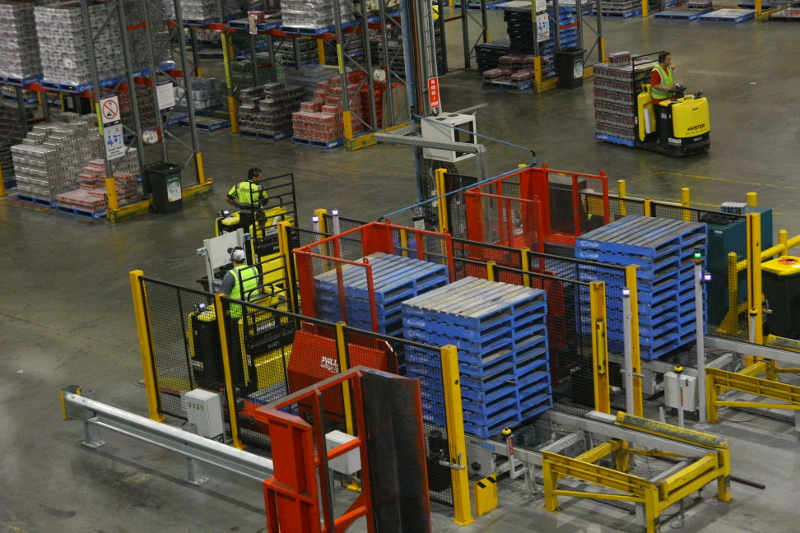
The tour then continued on to various parts of the distribution centre. We were exposed to how the returns system would work (an arduously manual task that cannot be easily automated), and how specific control systems were used in the automatic shrink wrap machine (excellent bondage tool by the way, if you’re into Saran Wrap :P). For example, the pallet loading system has to be very accurate as the variance tolerance for a fully loaded pallet is 0.8%. Yes, 0.8%. As in 0.008 of the pallet mass. This is in the kinda-crazy-nuts level of quality control.
Also, during the trip, I learned that at every step of the way, Coca Cola Amatil optimizes the process, and sometimes there would be conflicts of optimization. For example, the warehouse workflow is optimized in such a way that it may occasionally interfere with the driver’s efficiency in unpacking and delivering the goods. For example, I know that Tip Top Bakeries packs their goods per-order – i.e. they pack their goods according to their customer’s orders. This allows for efficiency when the driver delivers, because all the driver has to do is unload the entire pallet for the customer. Coca-Cola Amatil does it differently – things are packed by product. This allows for the distribution centre to be highly optimized. Whatever reason it is for this optimization, the tour did not cover.
CCA also are very very thorough with safety. As previously mentioned, everyone has to wear a high visibility vests. We had to take a test before even being allowed into the floor. Pedestrians have designated walk zones, and there was not a single soul walking where there are forklifts. Signs and warnings are also plentiful in the warehouse. The reason this struck me as odd is because I have never once walked into a place where there was a safety-related sign or warning or instruction within sight and hearing distance, no matter where I looked.
There isn’t much else to say really. The entire trip had been filled with tiny little nuggets of factoids that are interesting in a How-It’s-Made way. I learned a lot. So from here on, are pictures of my trip, with some small descriptions at the bottom: